Smart manufacturing or Industry 4.0 is a concept that is revolutionising Industrial processes. Manufacturing as we all know is often seen as the backbone of thriving economies worldwide. Recently, it has been fascinating observing the radical transformations manufacturing is undergoing.
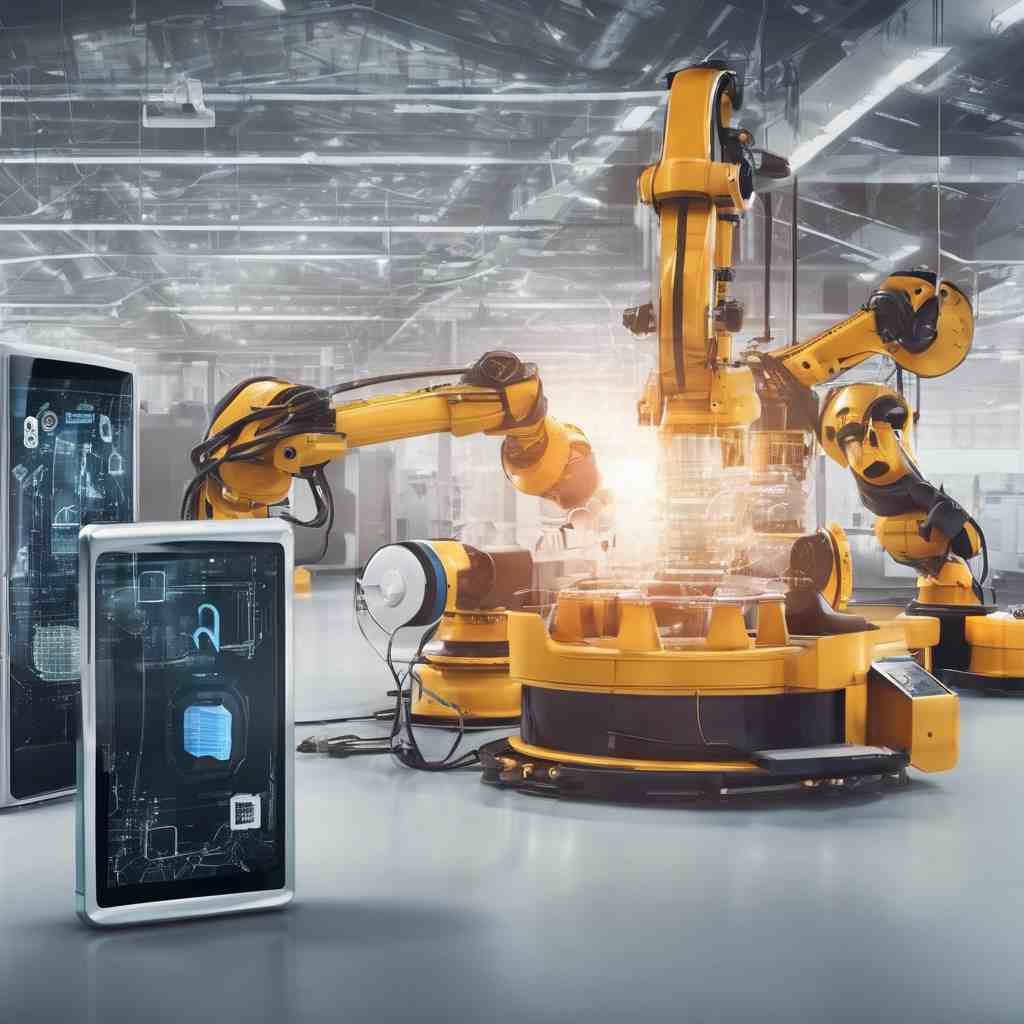
Geared by technological advancements, evolving consumer demands, and global pressures, the future of manufacturing promises to be drastically different from its past and the future is looking even smarter.
Every aspect of the industry is being re-designed and re-imagined from the factory floor to the boardroom. This post will delve into the key trends and technologies that are shaping the future of manufacturing, offering insights into what businesses can expect and how they can prepare for the changes ahead.
- The Rise of Smart Manufacturing
At the heart of the manufacturing revolution lies the concept of “smart manufacturing” or “Industry 4.0.” This paradigm shift leverages digital technologies to create interconnected, intelligent, and autonomous manufacturing systems. It’s not just about automation; it’s about connecting machines, data, and people in a seamless ecosystem.
A. Industrial Internet of Things (IIoT): Sensors embedded in machines, equipment, and products generate vast amounts of data. The process begins with the deployment of sensors and connected devices on machinery, equipment, or environmental points. This enables smart manufacturing.
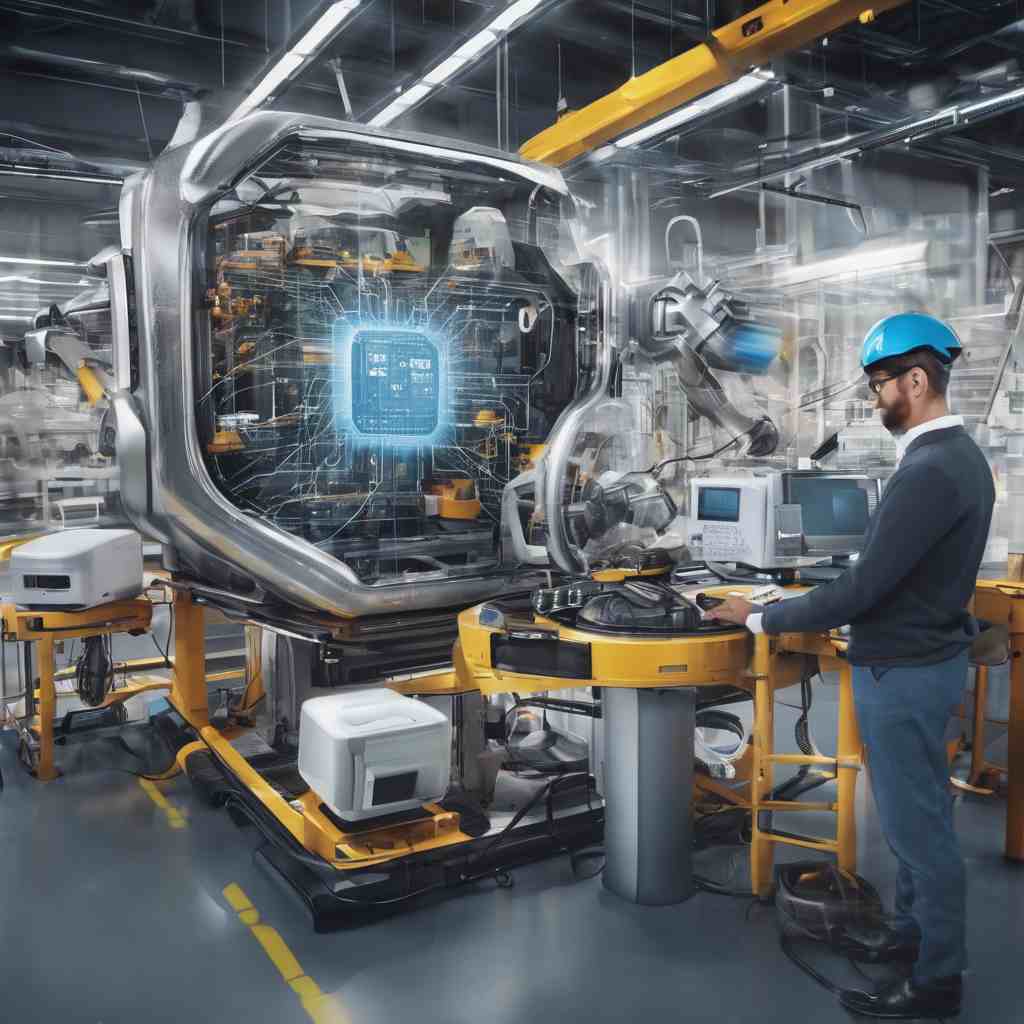
These sensors collect real-time data such as temperature, vibration, pressure, location, or other operational parameters.This data, transmitted through the IoT, provides real-time insights into performance, efficiency, and potential problems.
Based on the insights gained, automated commands can be sent back to machinery to adjust settings or trigger actions such as shutting down a machine, ordering maintenance, or alerting personnel. Predictive maintenance, optimized processes, and improved product quality become achievable goals with the advances of IoT.
C. Artificial Intelligence (AI) and Machine Learning (ML): AI and ML algorithms analyze the data collected from IIoT devices to identify patterns, predict failures, and optimize processes. AI-powered robots can perform complex tasks with greater precision and efficiency, while ML models can forecast demand, manage inventory, and personalize product offerings.
Introducing AI and ML to industrial processes is fast becoming be the core of smart manufacturing or industry 4.0.
D. Cyber-Physical Systems (CPS): CPS integrates physical processes with computational resources. These systems allow for real-time monitoring and control of manufacturing processes, enabling faster response times and improved efficiency. For example, a CPS could detect a potential machine failure and automatically adjust production schedules to minimize downtime.
Impact: Industry 4.0 promises increased productivity, reduced costs, improved product quality, and greater flexibility. Businesses that embrace these technologies can gain a significant competitive advantage by optimizing their operations and responding quickly to market changes.
2. Additive Manufacturing (3D Printing) Revolution
Additive manufacturing, also known as 3D printing, is really transforming the way products are designed and manufactured. Unlike traditional subtractive methods that remove material to create a part, additive manufacturing builds objects layer by layer, using materials like plastics, semiconductors, metals, ceramics, and composites.
Rapid Prototyping: 3D printing allows manufacturers to quickly create prototypes of new products, enabling faster design iterations and reduced development costs.
Customization and Mass Personalization: 3D printing enables the production of customized products tailored to individual customer needs. This opens up new possibilities for mass personalization, where products are mass-produced but personalized to meet specific requirements.
On-Demand Manufacturing: 3D printing allows manufacturers to produce parts on demand, reducing the need for large inventories and enabling faster response times to customer orders.
New Materials and Processes: Advancements in materials science are expanding the range of materials that can be used in 3D printing, enabling the creation of products with unique properties and functionalities.
Impact: Additive manufacturing is disrupting traditional manufacturing processes, enabling greater flexibility, customization, and speed. It’s also opening up new opportunities for product innovation and the creation of products with complex geometries that were previously impossible to manufacture.
3. The Rise of Robotics and Automation
Robotics and automation have been a part of manufacturing for decades, but recent advancements are driving a new wave of adoption. Collaborative robots (cobots) are designed to work alongside humans, while autonomous mobile robots (AMRs) can navigate factory floors without human intervention.
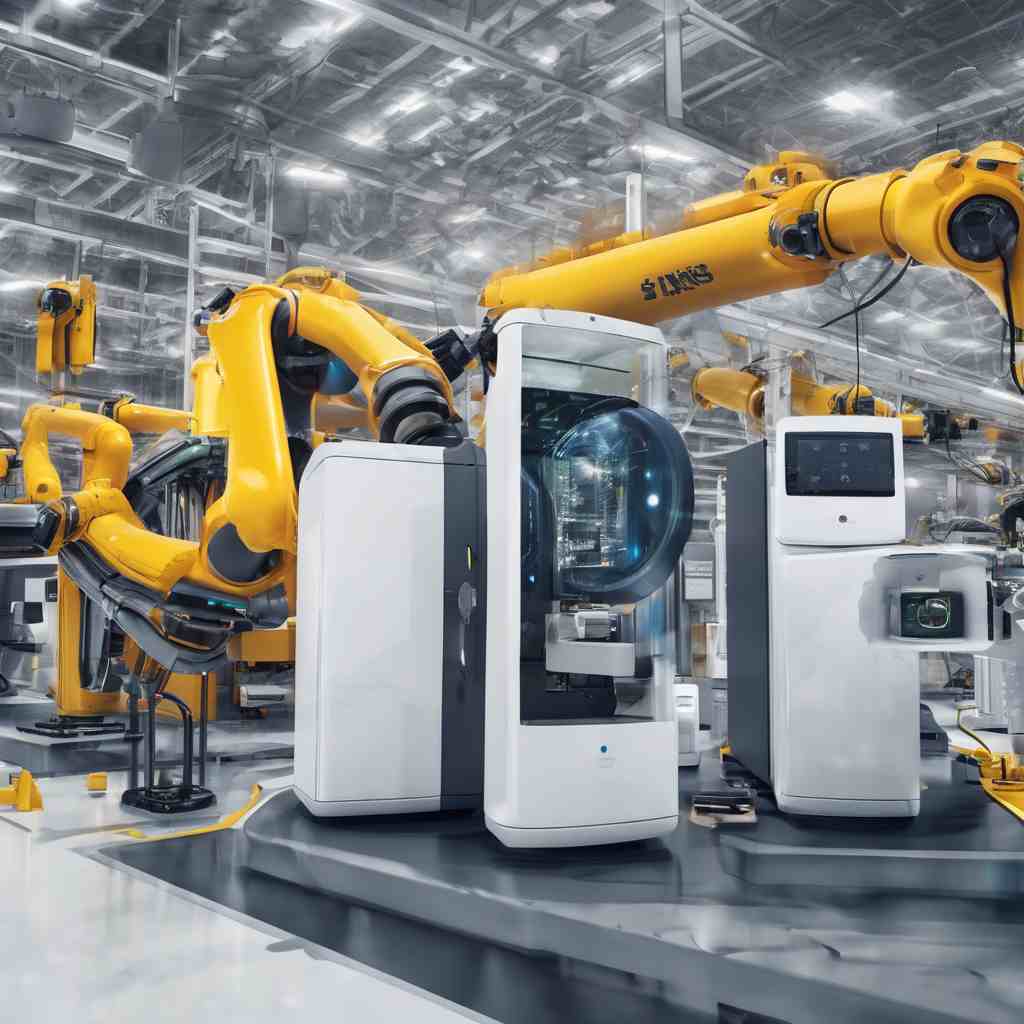
Cobots: Cobots are designed to work safely alongside humans, performing tasks that are repetitive, dangerous, or require high precision. They can be easily programmed and reprogrammed, making them ideal for flexible manufacturing environments.
AMRs can navigate factory floors without human intervention, transporting materials, parts, and finished products. They use sensors and software to avoid obstacles and optimize routes, improving efficiency and reducing labor costs.
AI-Powered Robots: AI is enabling robots to perform more complex tasks, such as visual inspection, quality control, and assembly. AI-powered robots can learn from experience and adapt to changing conditions, making them more efficient and versatile.
Impact: Robotics and automation are increasing productivity, reducing labor costs, and improving safety in manufacturing environments. As robots become more intelligent and versatile, they will play an increasingly important role in the future of manufacturing.
4. Sustainable Manufacturing Practices
Environmental concerns are driving a growing focus on sustainable manufacturing practices. Manufacturers are under pressure to reduce their environmental impact, conserve resources, and minimize waste.
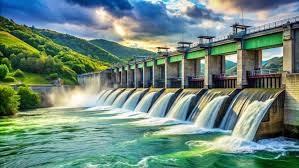
Circular Economy: The circular economy aims to eliminate waste and pollution by keeping materials in use for as long as possible. Manufacturers are adopting circular economy principles by designing products for durability, repairability, and recyclability.
Resource Efficiency: Manufacturers are implementing strategies to reduce their consumption of energy, water, and raw materials. This includes using energy-efficient equipment, optimizing manufacturing processes, and reducing waste.
Green Supply Chains: Manufacturers are working with their suppliers to reduce the environmental impact of their supply chains. This includes sourcing materials from sustainable sources, reducing transportation emissions, and implementing environmentally friendly manufacturing processes.
Waste Reduction and Recycling: Manufacturers are implementing programs to reduce waste and increase recycling rates. This includes implementing lean manufacturing principles, using closed-loop recycling systems, and finding new uses for waste materials.
Impact: Sustainable manufacturing practices are not only good for the environment but also good for business. By reducing costs, improving efficiency, and enhancing their reputation, manufacturers can gain a competitive advantage in the marketplace.
Consumers are increasingly demanding sustainable products, and businesses that can meet this demand will be well-positioned for success.
5. The Importance of Data Security and Cybersecurity
As manufacturing becomes increasingly connected, data security and cybersecurity become critical concerns. Manufacturers are vulnerable to cyberattacks that can disrupt operations, steal intellectual property, and compromise sensitive data.
Data Encryption: Data encryption is a process of converting data into an unreadable format, protecting it from unauthorized access. Manufacturers should encrypt data both in transit and at rest.
Access Control: Access control restricts access to sensitive data and systems to authorized personnel only. Manufacturers should implement strong access control policies and procedures.
Intrusion Detection and Prevention Systems: Intrusion detection and prevention systems monitor networks and systems for malicious activity and automatically block or mitigate attacks.
Security Awareness Training: Security awareness training educates employees about cybersecurity risks and how to protect themselves from attacks.
Impact: Cybersecurity is essential for protecting manufacturing operations, intellectual property, and sensitive data. Manufacturers must invest in cybersecurity measures to mitigate risks and ensure the continuity of their business.
6. The Evolving Workforce
The future of manufacturing will require a skilled workforce with new capabilities. As automation and AI transform manufacturing processes, workers will need to adapt to new roles and responsibilities.

STEM Education: STEM (Science, Technology, Engineering, and Mathematics) education is crucial for preparing students for careers in the future of manufacturing.
Upskilling and Reskilling: Manufacturers need to invest in upskilling and reskilling their workforce to ensure that workers have the skills needed to operate and maintain advanced manufacturing technologies.
Lifelong Learning: The pace of technological change is accelerating, and workers will need to embrace lifelong learning to stay current with new skills and technologies.